【クリエーターたち】国立研究開発法人産業技術総合研究所 阿多誠介 インタビュー
社会課題の最前線で、新しい材料の研究開発を通じて社会に貢献し続ける研究者たち。未来の日常を実現するために新たなチャレンジを続ける彼らの、想いと軌跡をひも解くインタビュー。
カタチや機能で表現される全てのモノは「何か」でつくられている。今回は、その「何か=素材や材料」を複合材料の視点で探求し続ける研究者、阿多誠介さんにお話を聞きました。
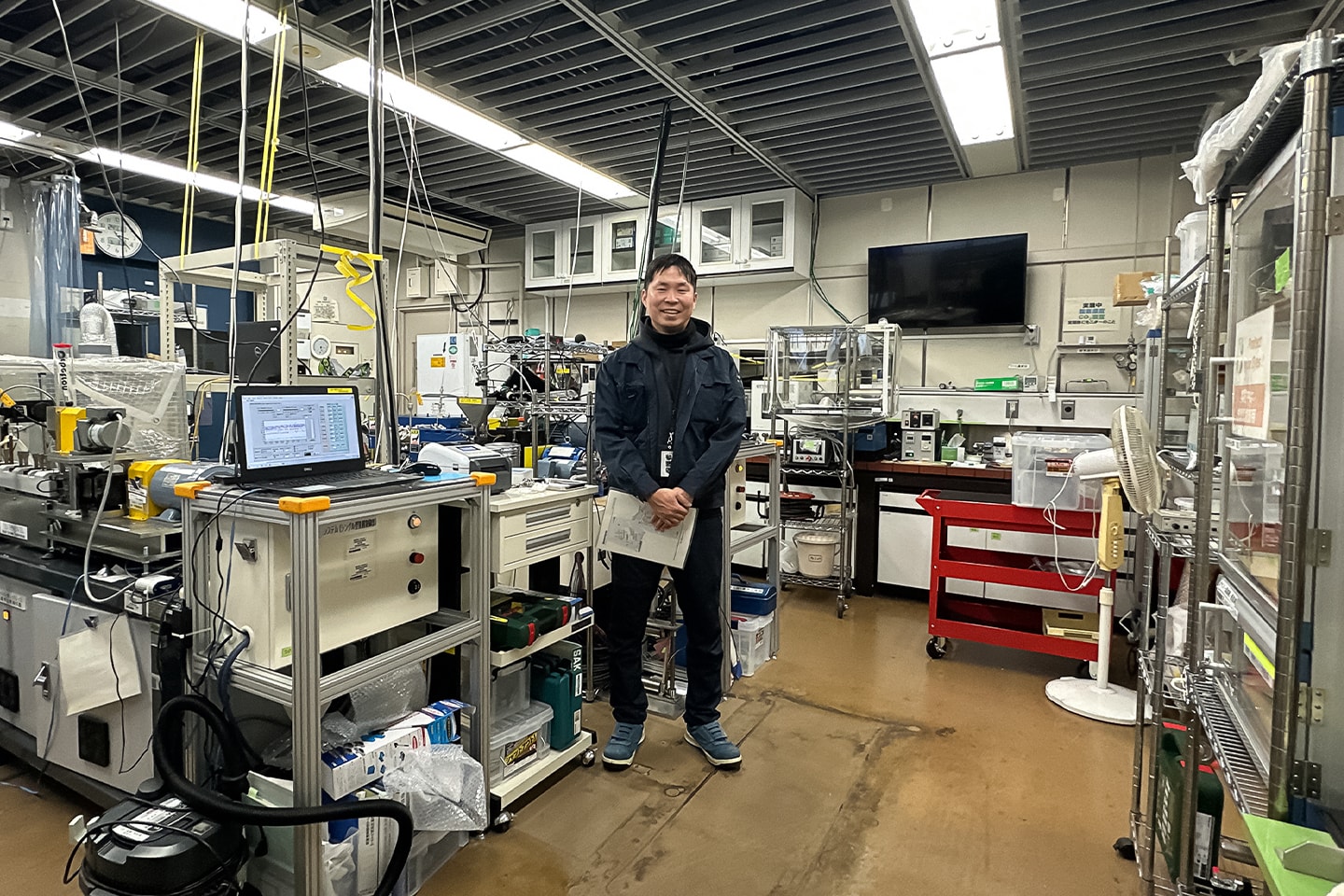
阿多・誠介(あた・せいすけ)
国立研究開発法人産業技術総合研究所 化学プロセス研究部門 スマートフロープロセスグループ主任研究員。東京工業大学在学時より、一貫して有機高分子の研究を続けて現在に至る。現在は、「プラスチックの成形加工分野でのDX活用について」、「バイオベースポリマーの実用化にむけての検討」そして「6Gを目指した材料開発」の3つのテーマに取り組んでる。
国立研究開発法人産業技術総合研究所
1882年に創設された農商務省地質調査所を発祥とし、以来140年以上にわたり国の経済や社会の発展に寄与するための研究活動を続けている。日本に3組織しかない特定国立研究開発法人の一つで、全国各地に12か所のネットワークを持ち、約2,300名(国内最大級)の在籍研究員と4,000名以上の外部人材が活躍している。年間共同研究契約数は約3,000件で、民間企業、大学、公的機関など、幅広く連携と協力を行っている。また産総研の技術は、高所調査ロボット、炭素繊維、メタンハイドレート生産技術、小型放射線線量計、メートル原器、津波調査など、身近なものに使われている。
この研究は、必ずどこかで誰かの役に立つ
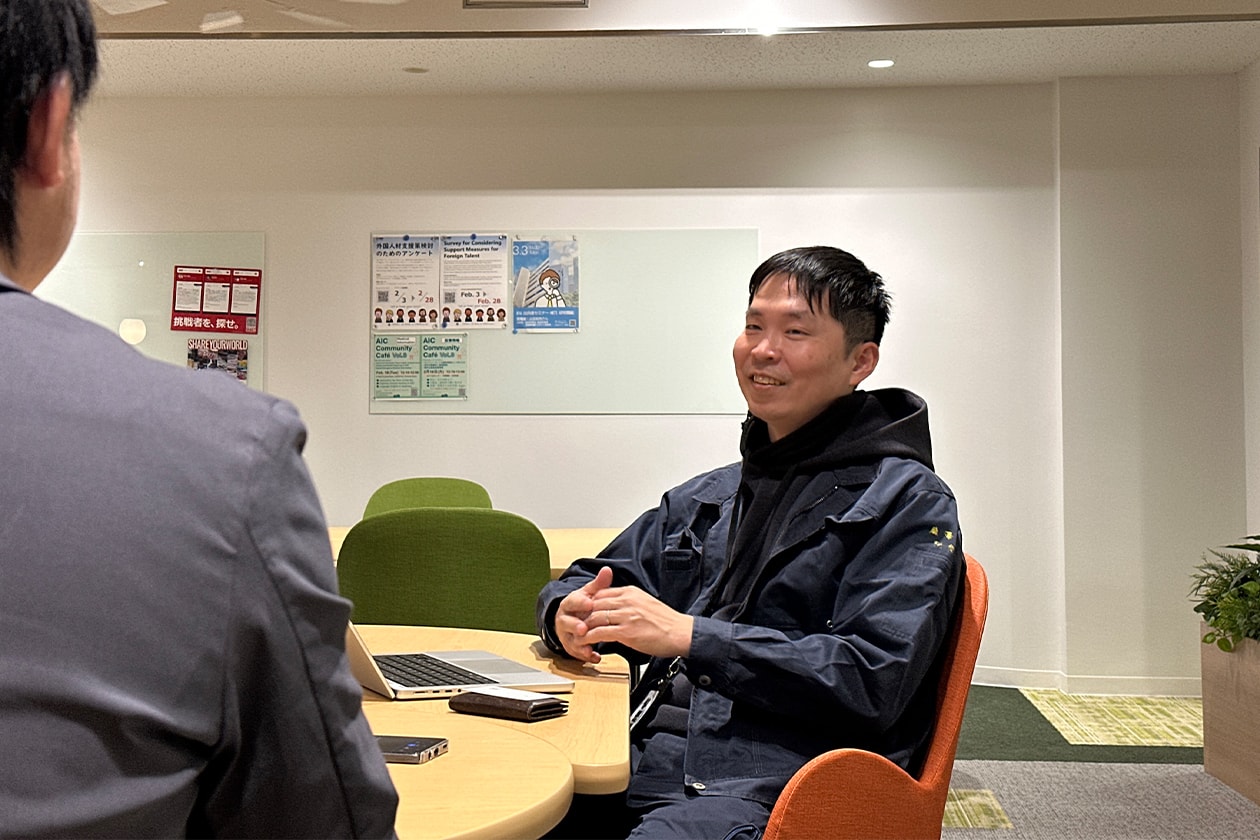
どうでしょう。一般企業への就職活動を全くしなかったわけではないんです。ただそこは時代の巡り合わせだったり縁だったりで、結局大学の修士から技術研修制度で来ていた産総研で、ポストドクターを経て自分の好きな道を歩くことになりました。この職場で仕事をすることも、ここでやらせてもらっている研究も、結果的にはよかったなと満足しています。
産業技術総合研究所(以下、「産総研」)のポジションって、大学と企業のちょうど中間なんです。役割でいうと、大学が基礎研究で企業が実用化。産総研はその橋渡しをするような立場で、応用寄りの研究をしています。それが自分には合っていると感じています。
それぞれ良さがありますよね。僕の場合は、興味があるだけでなく「誰かが必要としていたり、具体的にどこかで役に立つ予定のあるテーマ」に取り組みたいなと感じるので、企業から要望を聞いて、そこにむけて応用研究をしていく今の役割が、自分には向いてるのかなって思います。
あと僕、材料屋なので。材料って分野は、なかなかダイレクトに役に立ったっていう手応えを持ちづらい気がしていて。だからこそ、より「どうやって役に立てるかな」って考えるのかもしれません。
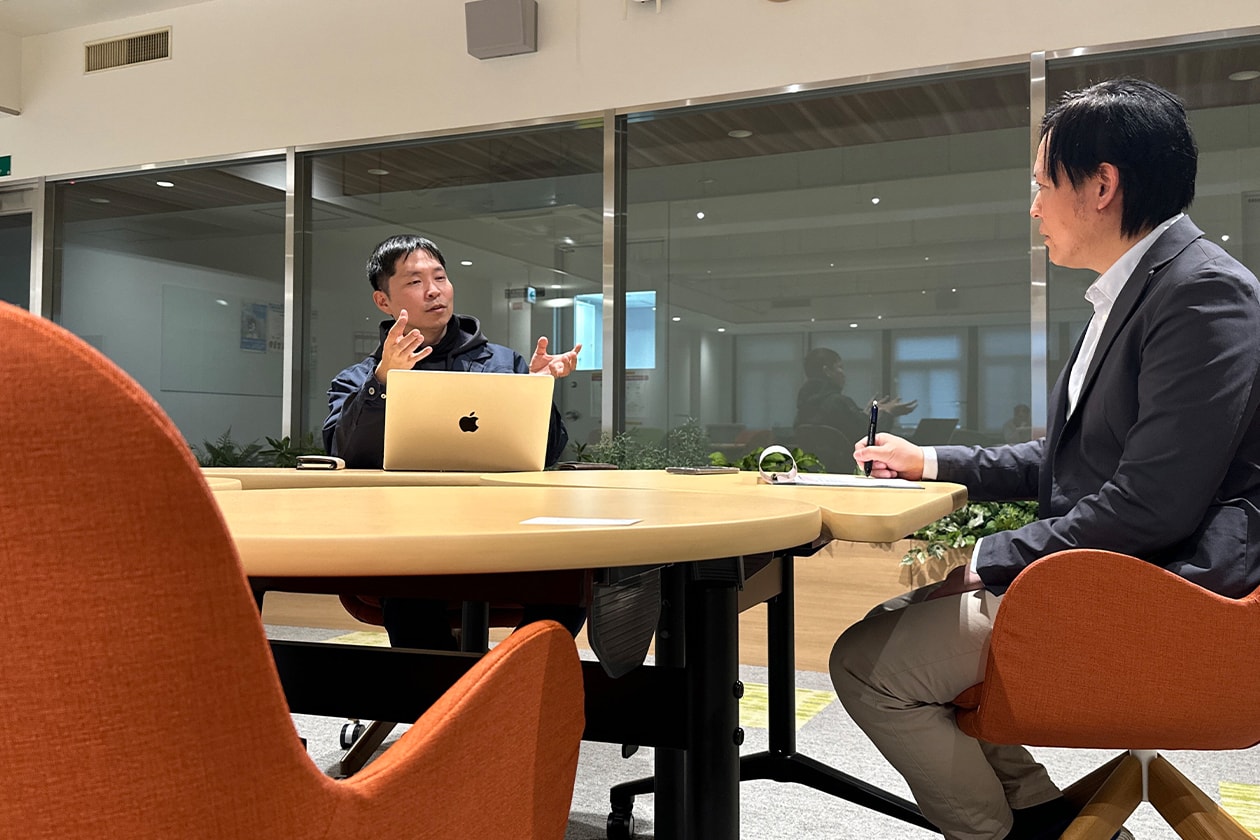
大まかにいうと3つのテーマがあって、まず「プラスチックの成形加工分野でのDX活用について」ですね。次に「バイオベースポリマーの実用化にむけての検討」もしています。そして「6Gを目指した材料開発」です。これらの研究に、同時並行で取り組んでる感じです。
新しい材料を作るときに「二軸混練」、つまり複数の材料を均一に混ぜ、分散・脱ガスしながら押し出す工程があるんですけど、この工程って結構ノウハウの塊みたいなところで。いままでは職人のようなひとが、匂いや光沢の具合で良し悪しを判断するやり方をしていたんです。けどこのやり方だとどうしても属人化してしまう。そこで、人が見ていた情報、いわゆる暗黙知といわれる情報を、形式知化する研究をしています。具体的には、計測器をつけてその中のデータを取ったり、画像データを色彩データに置き換えるなどして「良いものってデータ的にはこうなんだ」というところを数値に置き換えて整理していくわけです。
そうですね。これをいろんな材料で展開して、汎用化していければと思っています。技術の継承が難しいとされてきた感覚的な部分をデータ化していくことで、人材育成の面でも役立つかなと考えています。
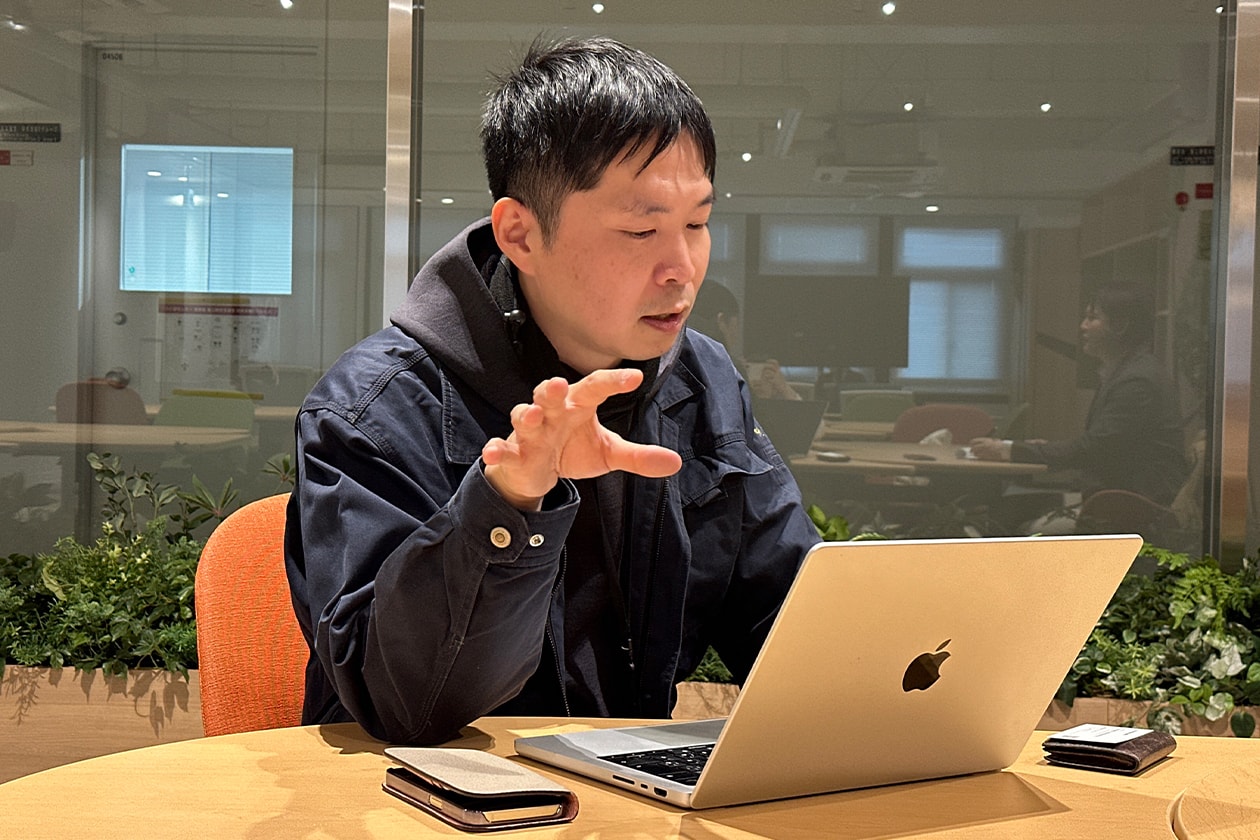
"熱硬化性"の樹脂をバイオベースポリマー、いわゆる植物や動物といった生物由来の原料から作ることができる、自然界のサイクルにしたがって循環が可能な材料に置き換えていく研究です。
たとえば"熱可塑性"の樹脂のように、成形品の廃材を粉砕して再成形する水平リサイクルができる場合は良いのですが、熱硬化性の樹脂だと簡単にリサイクルができないんです。身近なところでいうと、車のタイヤなども熱硬化性の樹脂を使っていますね。これをものすごいエネルギーをかけて無理やりリサイクルしてもエネルギーの無駄になってしまう。そこで、たとえば僕らが取り組んでいる内容だと、クリアコートのエポキシ樹脂をバイオ化できないかとか、ウレタン樹脂の硬化剤をバイオ化材に代替できないかといったことを、ドイツの生産技術研究所と共同で研究しています。
例えば食品残渣って今問題になってるじゃないですか。日本酒をつくったときに出る酒粕はどうするの、みたいなことです。酒粕って消費量が減ってるのに生産量は増えてるんです。処理の費用負担が大きいため、問題になっているわけです。あとキノコを栽培するときに使う廃菌床とかもそうです。そういったバイオマス材をバイオ化して再利用する動きが増えてきています。インドだと砂糖を作るときに出る廃糖蜜を使えないかっていうので、実際に日本の化学メーカーが従来のものよりも性能の良い材料をつくったという実績があります。
過去200年間くらいは、何でも「石油」で作られてたわけじゃないですか。それが、バイオ化によって「糖」に置き換えられるってなったときに、さらに高分子の可能性が広がってくる気がしますね。
高速伝送の場合、回路基板の誘電率が問題になってきます。5Gの場合で28GHzまで使っていると思うんですけど、さらに高周波のSub-THz(サブテラヘルツ)、100GHzから300GHzくらいの周波数帯に対応するには、回路基板に使う絶縁材料が低誘電材料である必要があるんですね。
これをフッ素でつくる方法があって、低誘電率の面ではすごくいいんですけど、それ以外の機能があまりよくないんです。接合する時に剥がれやすいし、加工性が悪いので表面が平滑にならない。
その点、僕らは発泡させる技術を持っているので、小さい泡を利用して低誘電材料を作ろうとしています。それでも、誘電率のばらつきがでてしまうので、うまく構造を制御して解決しようとしているんですけどね。
あなどれない前後工程とのコンビネーション
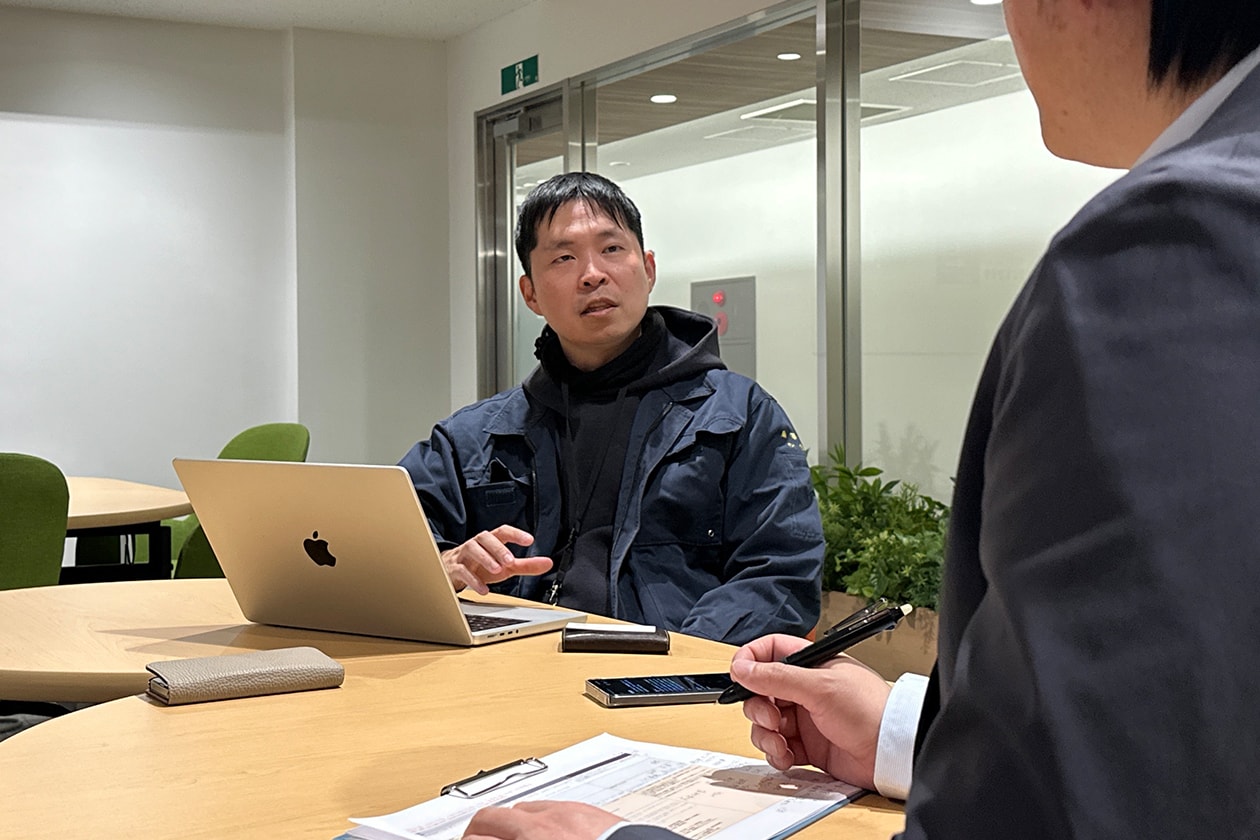
高分子材料の場合、基礎研究から始まって実用化にたどり着く過程で「生産スケールの壁」にぶつかります。生産スケールっていうのは、使う材料の量のことです。それが研究の初期段階の合成部門、その次に位置する僕らの材料を混ぜる部門、そして最後の成形部門でそれぞれケタが違うくらい使う材料の量に差があるんです。中間に位置する僕たちの材料を混ぜる部門にとってはけっこう悩ましい壁です。
そうなんです。最初は材料を合成する部門からスタートするわけですけれど、そこで使われる材料の量はせいぜい2~3グラムといったところです。それが成形部門では3キロとかになるんですね。僕たちはその中間にいるんですが、使う材料は数十~数百グラムといったところでしょうか。
合成部門は「新しい材料」をつくることを第一に考えています。でも実際に成形部門で千倍の量を扱うときに、設備や手順の都合で、そのまま問題なくできるとは限らないんです。
僕らは両者の間でものを混ぜるプロセスにいるわけですけど、双方の都合を考えながらの対応がとても難しいところですね。
私たちは最終的に実用化されることを目指しているので、スケールの壁は材料の金額の面でも立ちはだかってくるんです。たとえば合成部門の人が「新しい材料を合成しました」ってプレスリリースして、企業の人が来て「これいくらですか?」ってなったときに「今だと1グラム100万ぐらいですかね」みたいな(笑)
企業はキロ200円くらいのイメージで来てるので、そのままだともちろん成立しません。だから僕たちの部門で、重要な成分を維持しながら全体のコストを抑えたり、ほかの素材と組み合わせて調整したりもしますね。
最終的には生産性だとか、これ売れるのか、とかの判断も加わってきます。さらに言えば安全性だとか、いろいろな規制関係も絡んできますね。僕たちの部門ではそういったところも含めて、実際に材料を流通させるうえで必要なことを細かく調べて調整や提案をしています。
新しい材料の生まれる場所
では、研究室にご案内しますね。
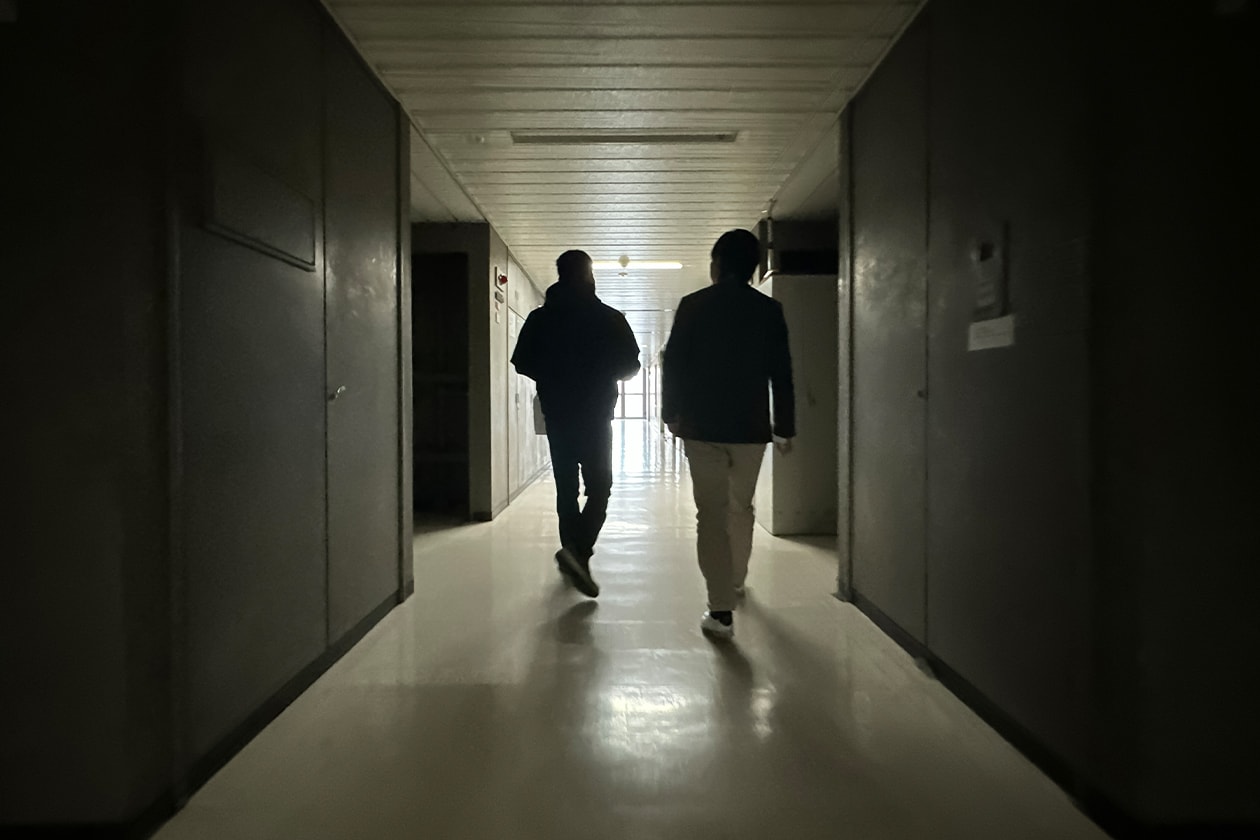
あと別棟にももう一箇所あって、そこには大きい設備類を入れてます。だいたい研究室を1人1部屋もらってて、この部屋は僕1人で使ってますね。ここを使ってもう2~3年かな。まえの研究室はもっと広くて。ひとりで8部屋とかありましたね(笑)
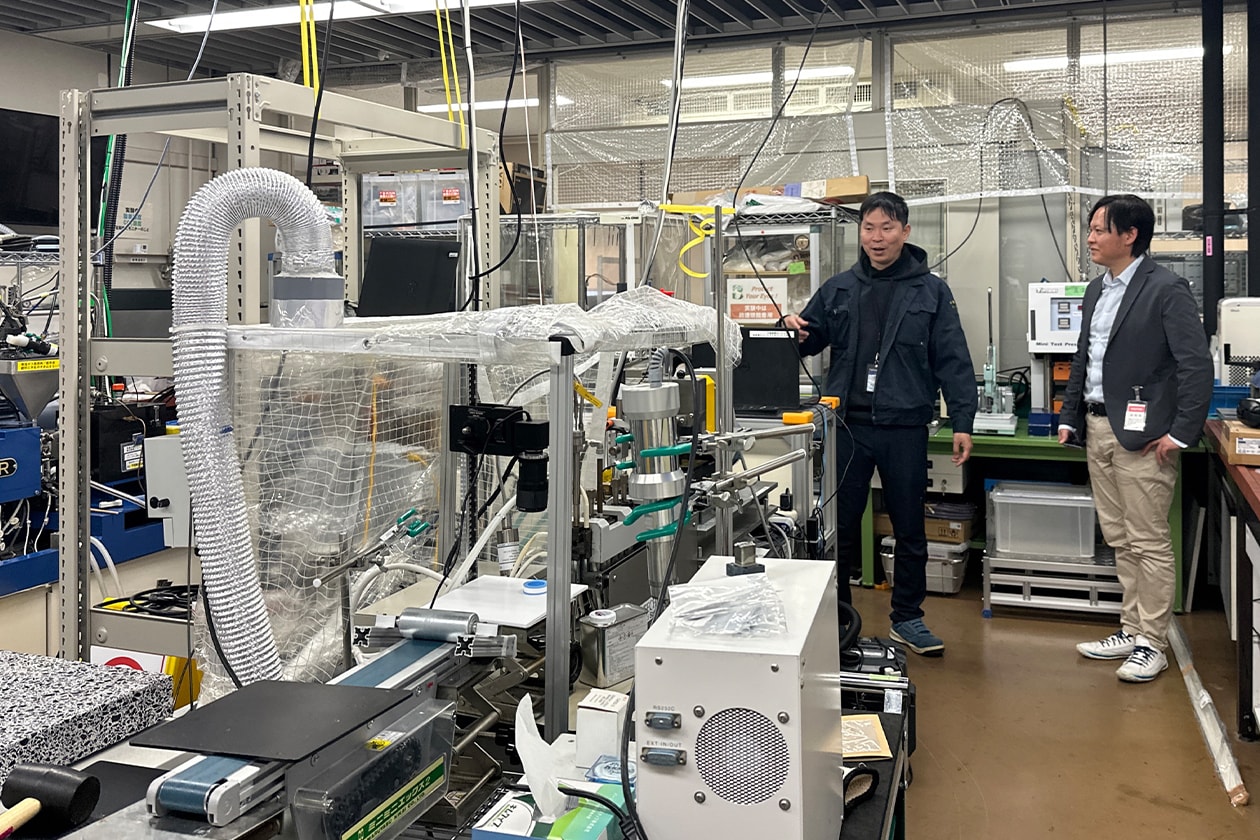
阿多さんの研究室には、さまざまな実験機器や計測機器が所狭しと並んでいました。
研究室内の装置やデータは、グラフィカルプログラミング環境を使って一元管理できるようにしています。データはもちろん装置自体も自動制御できるので、装置を増設してもここに繋げれば同じように一元管理することができます。
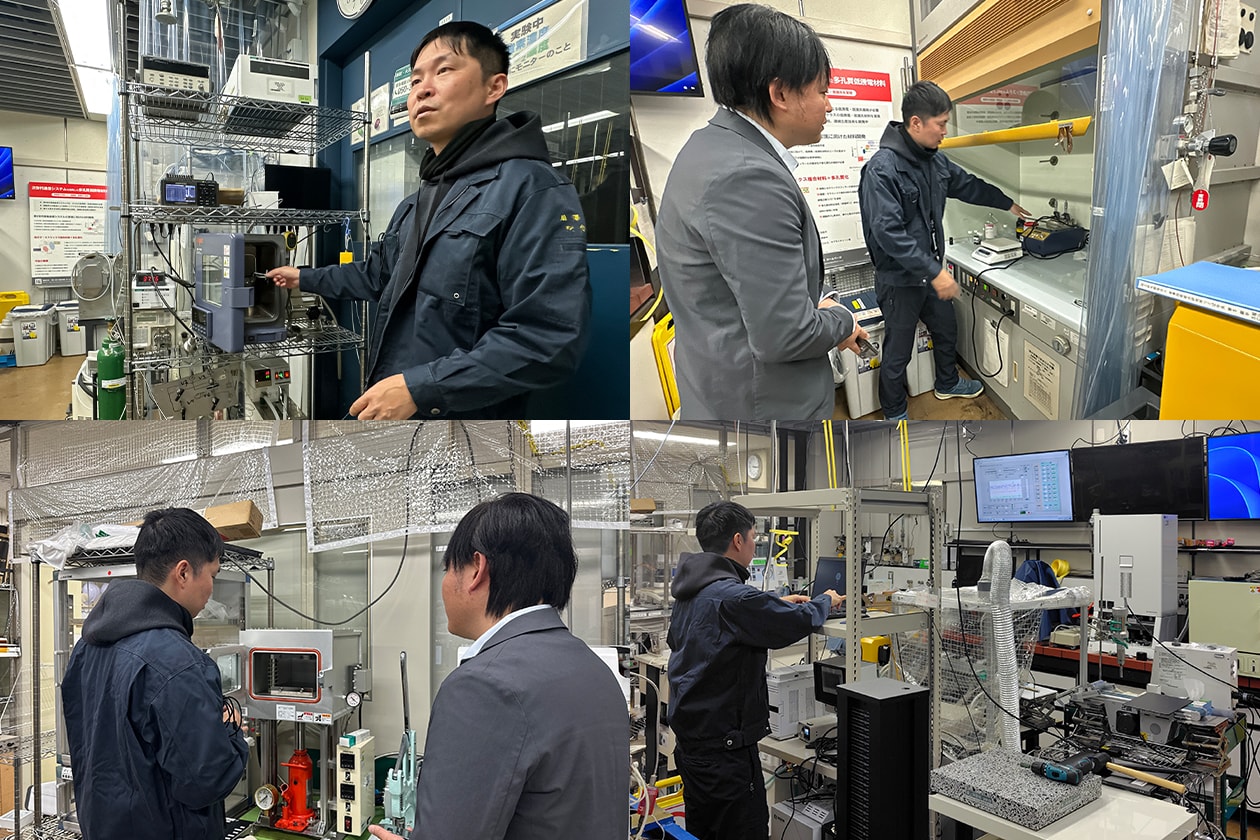
ひとつひとつの機材と実験の仕方を丁寧にご説明いただきました。
とくに手動のやつ(手動式INARI F06)は、バイオベースポリマーなんかでよく使っています。先ほど話したように、僕らが使う材料は本当に量が少ないので、今やっている試作には手動のやつがちょうどいいんです。10グラムくらいでできるので。どんどん簡単に試せるし、材料のロスを減らせるのが大きいです。
そうですね。現在はちょっと改造して使ってます。型を乗せるテーブルに治具を設置して、型の位置合わせがいらないようにしました。クランプスクリュー部分も、ワンタッチで型の固定ができるようにしました。僕らが使用する金型は今のところ決まった2種類のみなので、それにあわせて最適化しました。
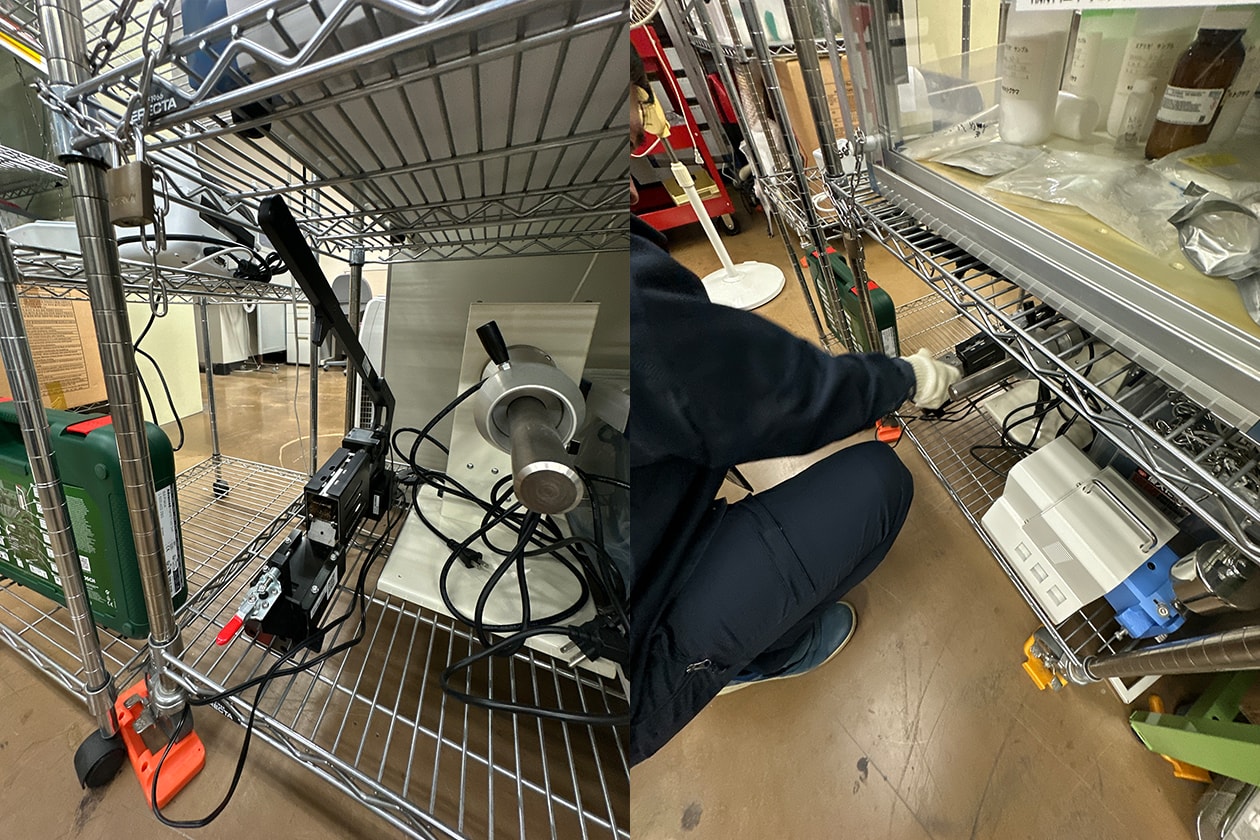
「手動式 INARI F06」を改造してご使用いただいていました。(後継機種「手動式 INARI M06」)
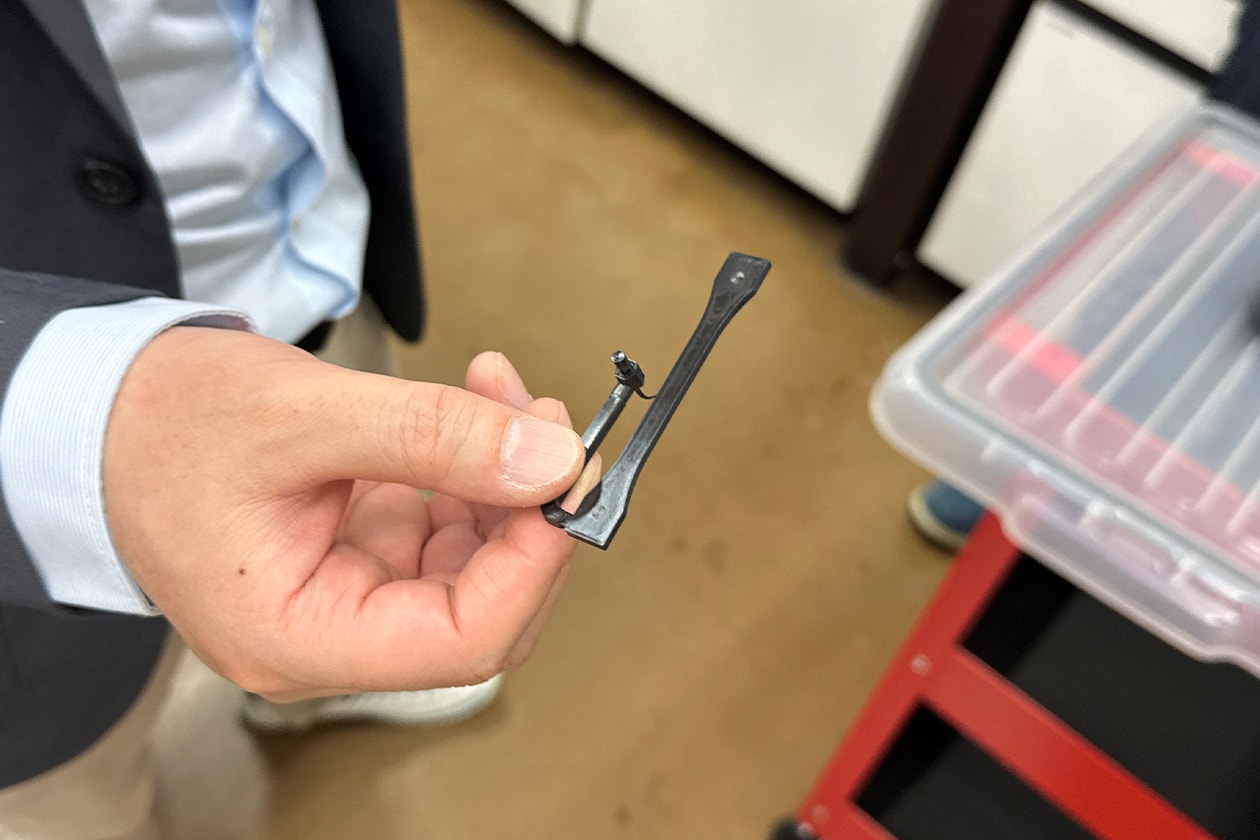
ポリプロピレンにカーボンナノチューブを混練したダンベル試験片を見せていただきました。(「手動式 INARI F06」で成形)
こちら(空圧式 INARI P35)は去年の秋に導入しました。今取り組んでいる研究の材料の量が、この機械の適正量に対してちょっと少な過ぎるので、まだ試し打ちをした程度です。来月入ってくる新しい材料が50グラムくらい使うものなので、その際に本格的に活用できるかなと思います。
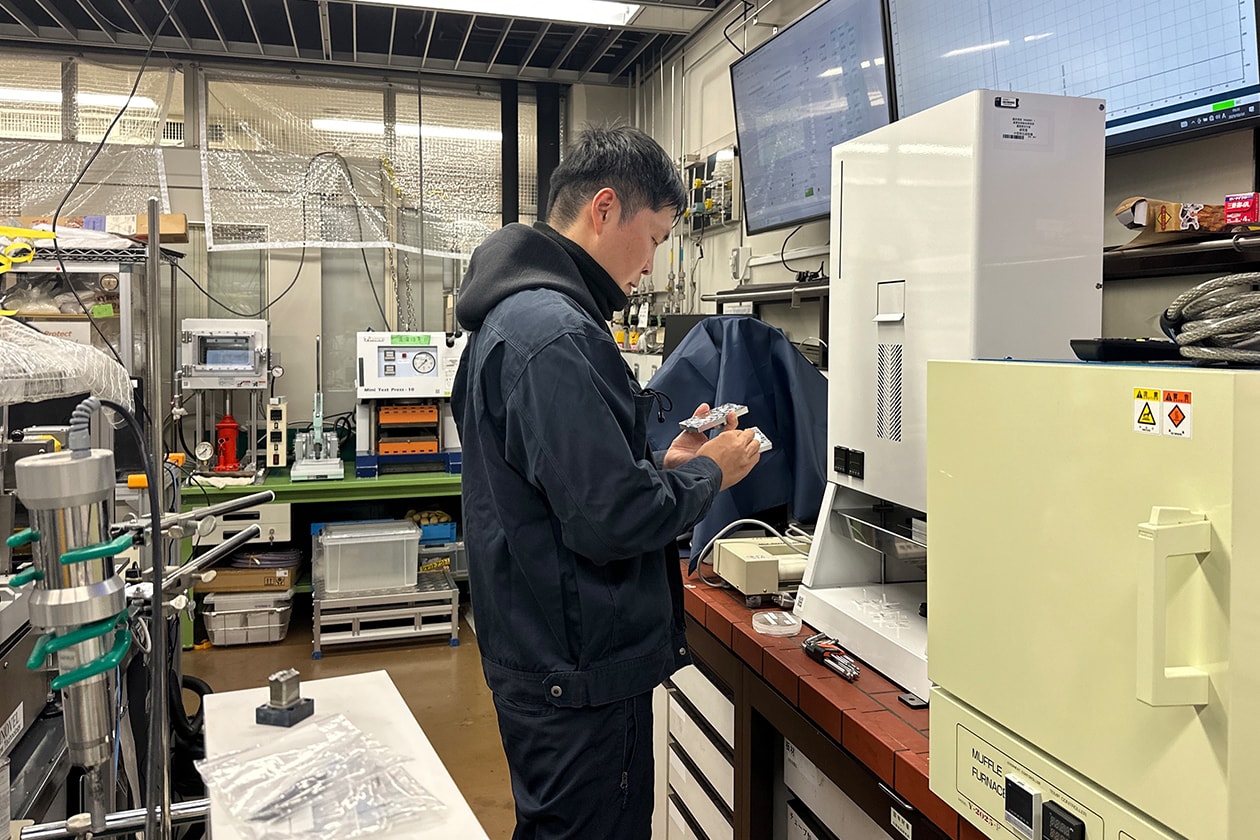
論文によって研究は世に放たれる
研究成果が実際に技術移転される時って答えるのが模範回答なんでしょうけれど、正直にいうと自分の論文が採択された時ですね。僕ら研究者なので、論文が通るとやっぱり嬉しいなって思います。それと予算が取れたときとかですかね。
論文が採択される前段階でピアレビュー(査読)というのがあるんですね。研究自体は最初から最後まで基本的に一人でやることが多いのですが、そんな中、ピアレビューで同業の研究者からコメントがくるんです。そこで初めてほかの研究者とコミュニケーションがとれるので、僕からするとそれは嬉しいことです。特にポジティブなコメントをもらうとやっぱり嬉しいですよね。指摘されたら修正もしながら、論文がさらに完成形に近づいていきます。
それと予算の獲得についてはいろんな枠があって。科学研究費助成事業だったら8月ぐらいに応募書類を書くんですけど、それが通ることで翌年自分が立案した研究に取り組めるので、これもやっぱり嬉しいですね。
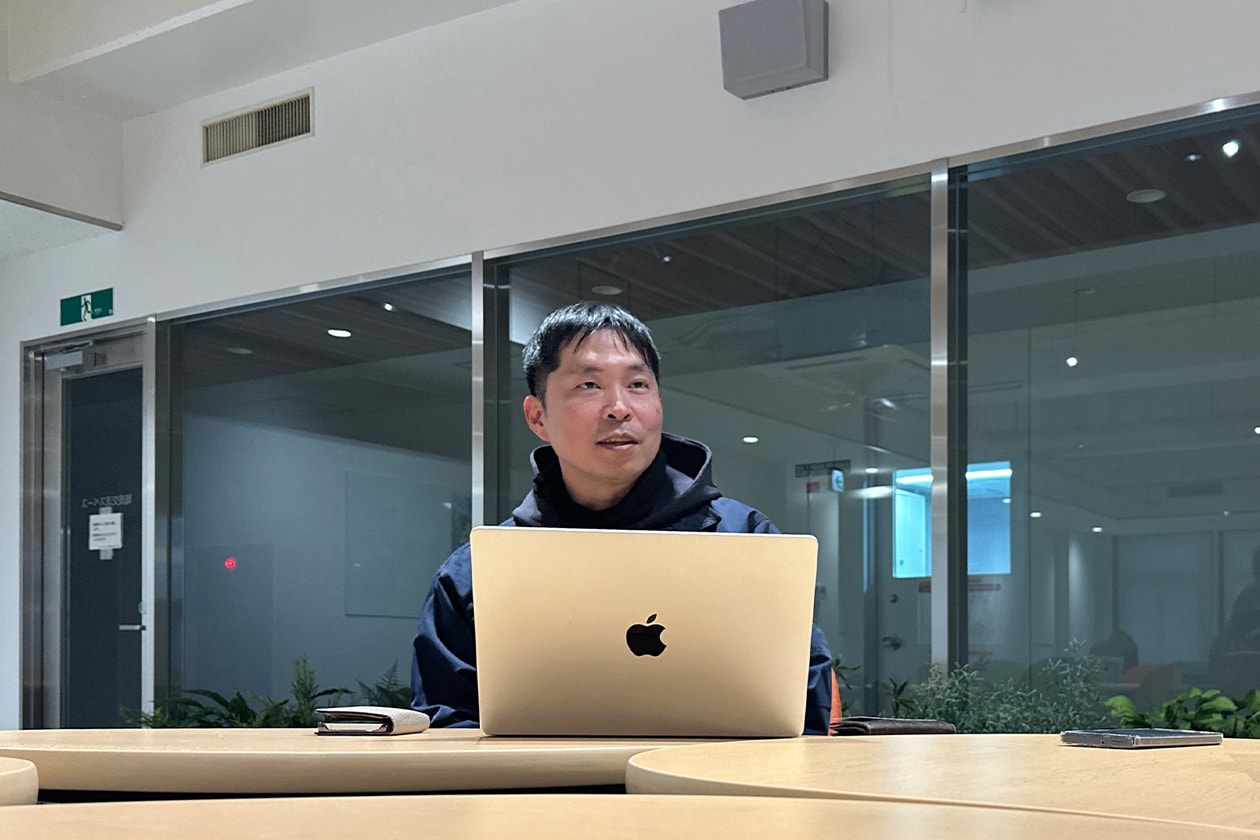
技術が移転されて実用化されるのはずっと先のことなんです。それこそ成形部門も経たその先のことなので、あまり実感がないっていうのが正直なところですね。
研究者からすれば手が離れてしまっているので、そのあとの生産プロセスや臨床はどうしても視野から外れてしまいます。だからこそ、安定して作れるとか品質が保証できるとか、そういったことも含めてちゃんと論文としてまとめていくのが自分たちの役目なんだと思います。
代表的な成果の一つで言えば カーボンナノチューブの入ったオーリング(SGOINT-Oリング)があって、これは製品化もされています。カーボンナノチューブというと補強のイメージがあるかもしれませんが、このときは補強剤というより酸化防止剤として入れました。部署の異動前の取り組みではありますが、自分も貢献した研究成果だと認識しています。
みんなでひとつのことに取り組みながら、ちょっとずつ領域をはみ出す。
高分子素材の研究分野は、実は最近研究者が減ってきているんです。僕が所属している成形加工学会の構成員も純粋な研究者は少数で、7割ほどを企業関係者が占めている状態です。この比率は、学会としては結構珍しくて。
研究者が減ってきている理由はいろいろあるのでしょうけれど、ひとつは研究対象として少し地味で実験もたいへんと見られてしまっているのかもしれません。ただ産業的にはすごく大事な分野なので、学会の活動を通じて人材育成にも携わって、少しでも高分子成形加工分野の研究を盛り上げていきたいと思っています。
あと学会自体の数はそこそこあるんですけど、その分バラバラに活動しちゃって分散している感じがあって。そこももう少しまとまって、一つの大きな動きがつくれるといいのかなと思います。
あと最近では、材料のことだけでなく機械のことや実装の話まで、さまざまな領域のことを分かっていないと話ができなくなってきているので、結構ジェネラリストっぽい人が要るのかなぁと思いますね。もちろん僕も本を買いあさったりしながら、常に新しい情報をいれるようにはしてます。
そういった流れの中にいると、僕も含めてそれぞれの専門分野に携わる人が集まってきて、みんなで1つのテーマに取り組めるってのが結構大事なのかな、と思ったりしますね。その中でみんながちょっとずつ自分の領域をはみ出していって、人の分野のことを勉強していくといいのかな、と思っています。
そうですね。僕は元々誰かの役に立つ研究に取り組むことがすきですし、私たち産総研のミッションも、科学技術によって社会課題を解決へと導くことです。そのためには、いつもすこし先を見据えていることが大事なのかなと思います。
とはいえ僕も最初から「未来を作る研究職につくぞ!」とか思っていたわけではなくて、たまたま入った大学が今の材料研究に近かっただけなんです。大学の1年次に有機と無機と金属のことを勉強して、2年にあがるときに学科の選択があって。父親に「どこが面白いかね」って聞いたら、「有機じゃない?」みたいな(笑)。当時父は電機メーカーに勤めていて、有機ELが盛り上がってくるぞっていうタイミングだったからそう言ったのかなと思うんですけど。「そっか」と思って有機を専攻して、修士から産総研に来るようになってしばらくした頃に、とあるリサーチに携わることになって。それがすごくおもしろくて、自分で勝手に研究テーマを立ち上げて研究をしていったんですけど、そのときに「自分はこういうことが好きかもしれないな」と思ったんです。そしてその延長線上に今があるような気がします。
要するに、いつも先に未来のことを考えてなにかしている、というよりは、そのときどきで興味が湧いたことに取り組んできて、そうしてたどり着いたのがたまたまいつも少し先のことを見据えているようなポジションだった、ということかなと思っています。なのでこれからもそんなかんじで、目の前の研究に取り組んでいけたら、と思っています。
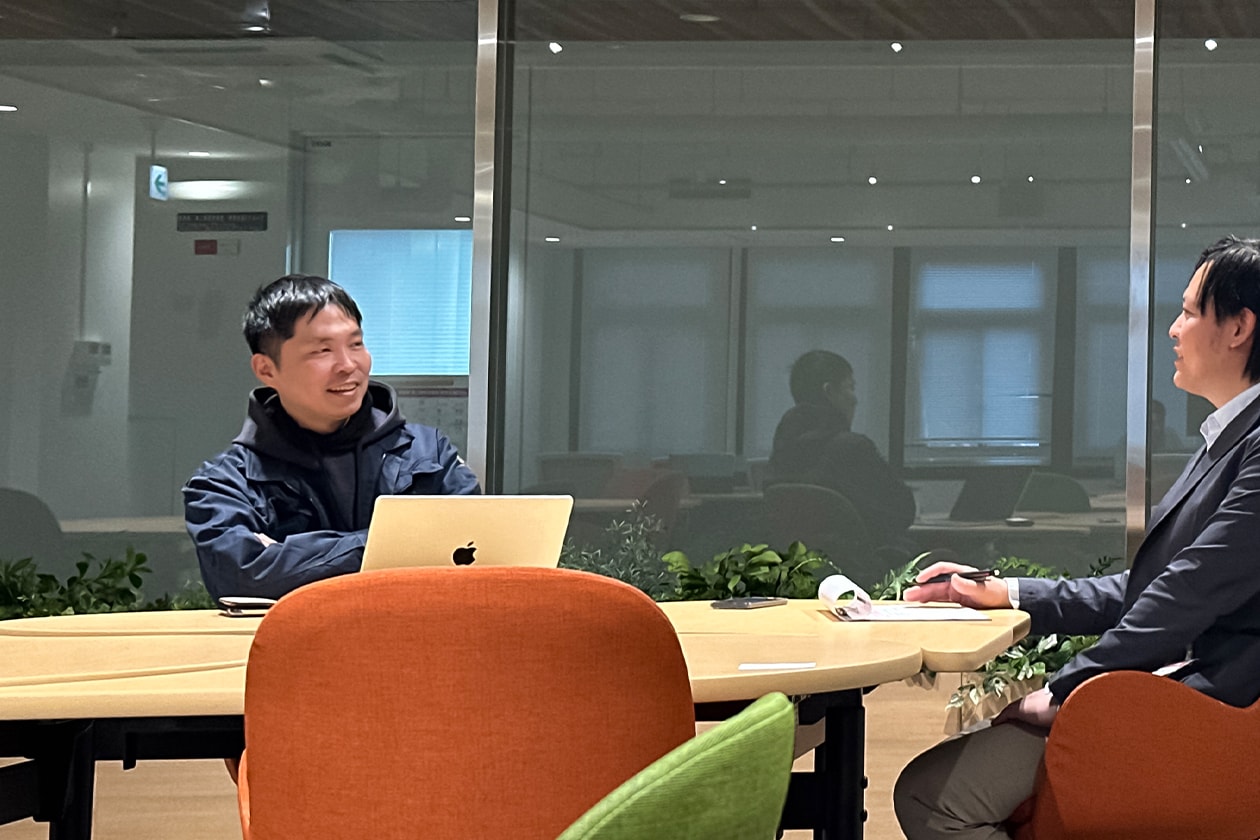
構成・写真:中村 良枝
インタビュー:小澤 聡
編集・ライティング:塚原 康徳
関連記事
【クリエーターたち】フジイオプチカル株式会社 藤井太 インタビュー
眼鏡のまち鯖江で、寸法では表すことのできない「良い眼鏡の感覚」を大切に、かけ心地やデザインを追求し続ける藤井太さんにお話を聞きました。